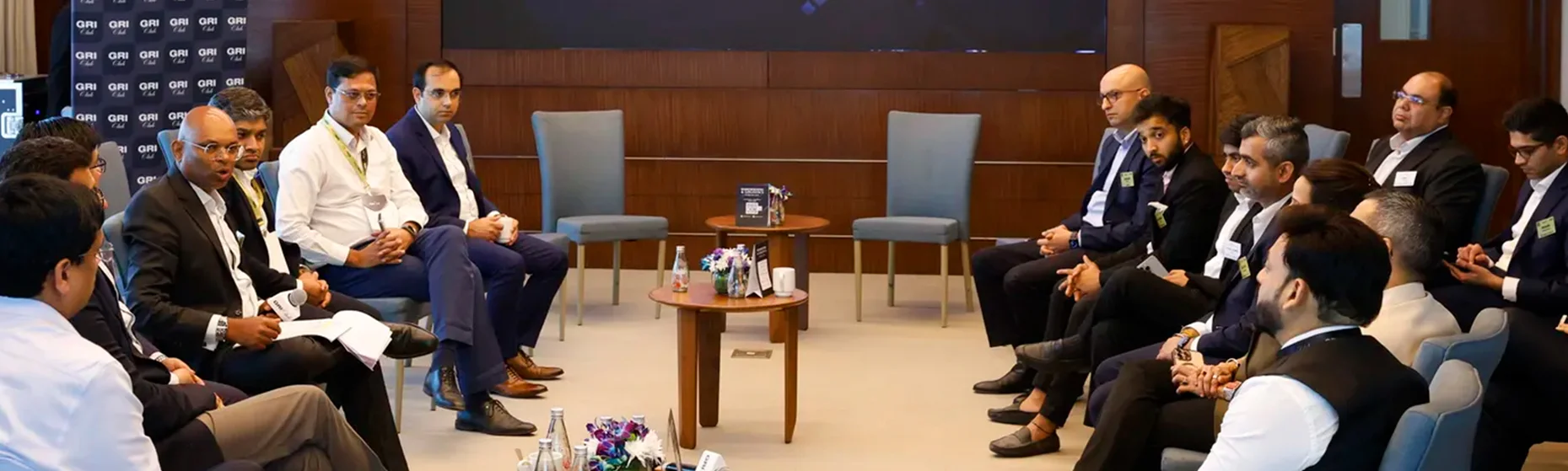
The rise of in-city warehousing amid India’s logistics revolution
Leading real estate experts on how demand shifts, regulatory challenges, and innovative strategies are reshaping urban logistics
July 3, 2025Real Estate
Written by Isabella Toledo
In-city warehousing offers undeniable advantages, particularly in supporting rapid last-mile delivery and maintaining proximity to consumers, which is essential for industries requiring fast, flexible delivery systems.
As a result, micro-warehouses have surged in densely populated cities, optimising last-mile delivery and reducing costs. These smaller facilities enable businesses to fulfil orders quickly, catering to consumers’ increasing desire for convenience.
Beyond e-commerce giants, the growth of omnichannel retail is also driving demand for in-city warehousing. Along with the rise of dark stores - dedicated solely to processing e-commerce orders - retailers are repurposing physical stores into fulfillment hubs to support both online and in-store sales.
This hybrid model maximises the use of existing infrastructure while meeting consumers’ growing demand for convenience through services such as "Click & Collect" and rapid delivery.
Despite these advantages, the model faces significant challenges. High land costs and complex regulatory hurdles make large-scale warehouse development within city limits difficult, limiting options for expansion.
Mumbai remains a key market, repurposing underused spaces like basements and old industrial buildings into logistics hubs. Areas such as Andheri and Bhiwandi attract investment in multi-use logistics serving e-commerce and retail, though balancing infrastructure needs with older buildings is challenging.
Bangalore’s growing tech and e-commerce sectors have embraced tech-driven micro-fulfilment centres, supported by EV-based last-mile delivery fleets that reduce emissions and ease congestion.
Tier 2 and 3 cities, including Lucknow, Jaipur, Indore, and Coimbatore, have also seen warehousing absorption rise, driven by local demand and better infrastructure. These locations offer cost-effective growth opportunities and will increasingly shape India’s warehousing landscape.
Unlike residential or commercial real estate, warehousing is not yet fully integrated into city planning regulations, complicating zoning approvals and land acquisitions for developers.
Residential and commercial land often offers higher development potential, leading developers to prioritise these uses over industrial and logistics facilities. This creates conflicts, as ideal warehousing locations are frequently zoned for residential or commercial purposes with higher land values.
While government initiatives, such as the National Logistics Policy, and state programmes offer some support, they have yet to fully address urban warehousing’s unique requirements and challenges.
Stakeholders face a key choice between CapEx-heavy models, involving significant upfront investments in land and construction, and approaches focused on operational expenditure (OpEx), which prioritise flexibility through leasing and operational expenses.
CapEx largely suits large firms with stable demand, while OpEx models are more likely to appeal to businesses needing scalability amid market uncertainty.
Innovative solutions include repurposing underutilised urban spaces, such as malls and industrial sheds, into cost-effective warehouses. Partnerships between developers and tenants also help share resources and reduce costs.
These initiatives are crucial for balancing the need for additional warehousing space with the rising costs of land and infrastructure. However, the long-term sustainability of these models remains a concern.
High operational costs in urban areas continue to make it difficult for businesses to achieve a return on investment that justifies the construction and upkeep of these facilities.
Advanced data analytics and artificial intelligence are playing a vital role in optimising route planning, forecasting demand, and improving supply chain management, while smart inventory systems provide real-time stock updates, allowing companies to better manage inventory and reduce the risks of stockouts and overstocking.
Automation technologies, such as robotic picking, sorting, and packing, further streamline operations by reducing labour costs and increasing throughput. This automation speeds up fulfilment processes and minimises human error, leading to more accurate and reliable deliveries.
Alongside operational gains, many companies are incorporating green technologies like solar-powered warehouses and energy-efficient systems. These sustainable innovations not only boost efficiency but also contribute to reducing the environmental impact of urban logistics.
In-city warehousing offers undeniable advantages, particularly in supporting rapid last-mile delivery and maintaining proximity to consumers, which is essential for industries requiring fast, flexible delivery systems.
Evolving retail and e-commerce demands
India’s logistics landscape is rapidly evolving due to the rise of e-commerce and quick-commerce players whose business models demand fast, efficient fulfillment. With same-day and next-day delivery becoming the norm, the need for decentralised, hyperlocal warehousing in urban centres has skyrocketed.As a result, micro-warehouses have surged in densely populated cities, optimising last-mile delivery and reducing costs. These smaller facilities enable businesses to fulfil orders quickly, catering to consumers’ increasing desire for convenience.
Beyond e-commerce giants, the growth of omnichannel retail is also driving demand for in-city warehousing. Along with the rise of dark stores - dedicated solely to processing e-commerce orders - retailers are repurposing physical stores into fulfillment hubs to support both online and in-store sales.
This hybrid model maximises the use of existing infrastructure while meeting consumers’ growing demand for convenience through services such as "Click & Collect" and rapid delivery.
Despite these advantages, the model faces significant challenges. High land costs and complex regulatory hurdles make large-scale warehouse development within city limits difficult, limiting options for expansion.
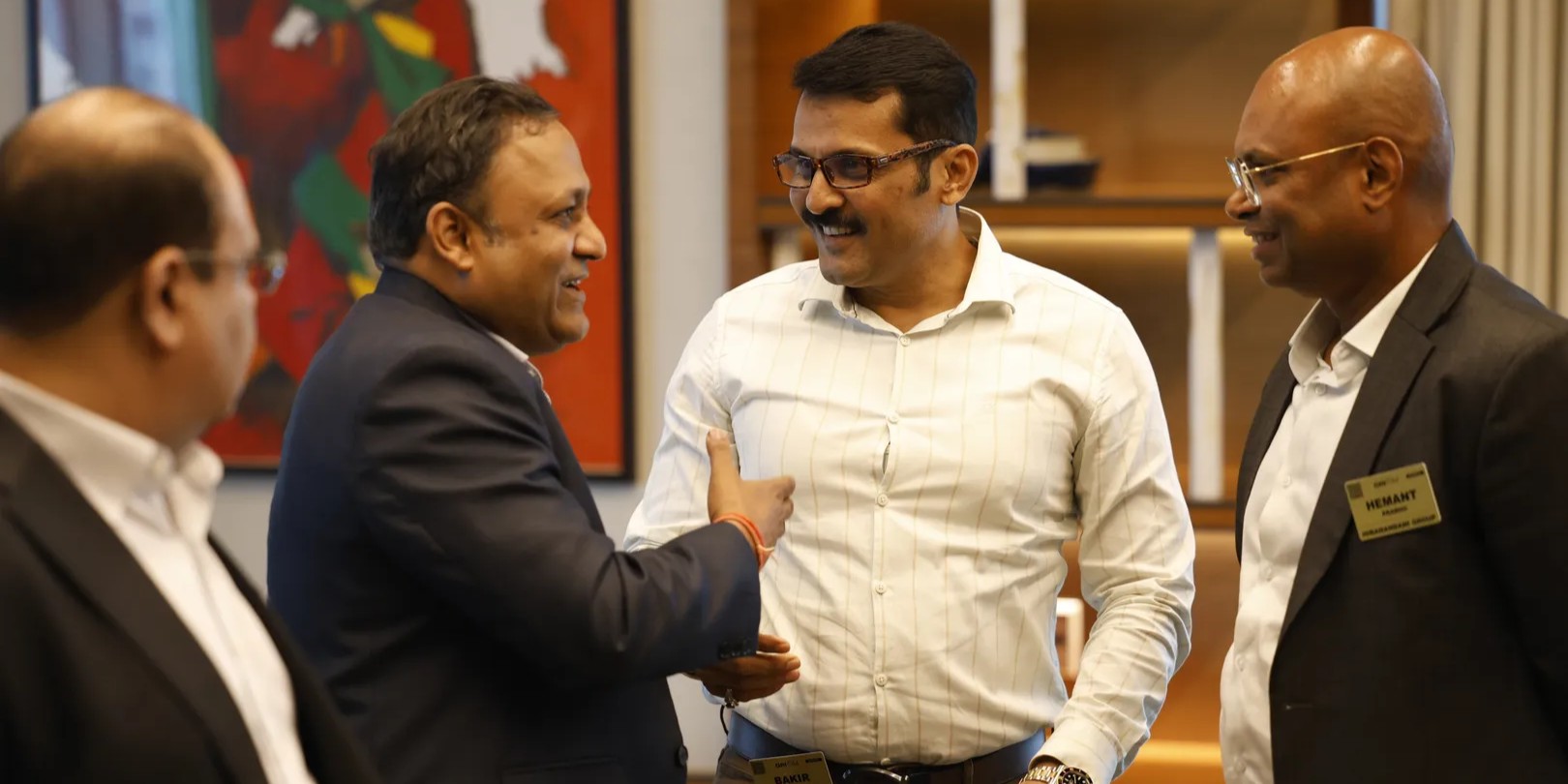
(GRI Institute)
Major hubs and emerging locations
While major metros continue to lead India’s warehousing sector, emerging cities are gaining importance as demand spreads beyond urban centres. The hub-and-spoke model is increasingly adopted, with warehouses on metro outskirts supporting smaller fulfillment hubs within cities.Mumbai remains a key market, repurposing underused spaces like basements and old industrial buildings into logistics hubs. Areas such as Andheri and Bhiwandi attract investment in multi-use logistics serving e-commerce and retail, though balancing infrastructure needs with older buildings is challenging.
Bangalore’s growing tech and e-commerce sectors have embraced tech-driven micro-fulfilment centres, supported by EV-based last-mile delivery fleets that reduce emissions and ease congestion.
Tier 2 and 3 cities, including Lucknow, Jaipur, Indore, and Coimbatore, have also seen warehousing absorption rise, driven by local demand and better infrastructure. These locations offer cost-effective growth opportunities and will increasingly shape India’s warehousing landscape.
Policy gaps and regulatory challenges
As urbanisation accelerates and last-mile delivery demand grows, the lack of dedicated zoning for warehousing has become a major challenge in India.Unlike residential or commercial real estate, warehousing is not yet fully integrated into city planning regulations, complicating zoning approvals and land acquisitions for developers.
Residential and commercial land often offers higher development potential, leading developers to prioritise these uses over industrial and logistics facilities. This creates conflicts, as ideal warehousing locations are frequently zoned for residential or commercial purposes with higher land values.
While government initiatives, such as the National Logistics Policy, and state programmes offer some support, they have yet to fully address urban warehousing’s unique requirements and challenges.
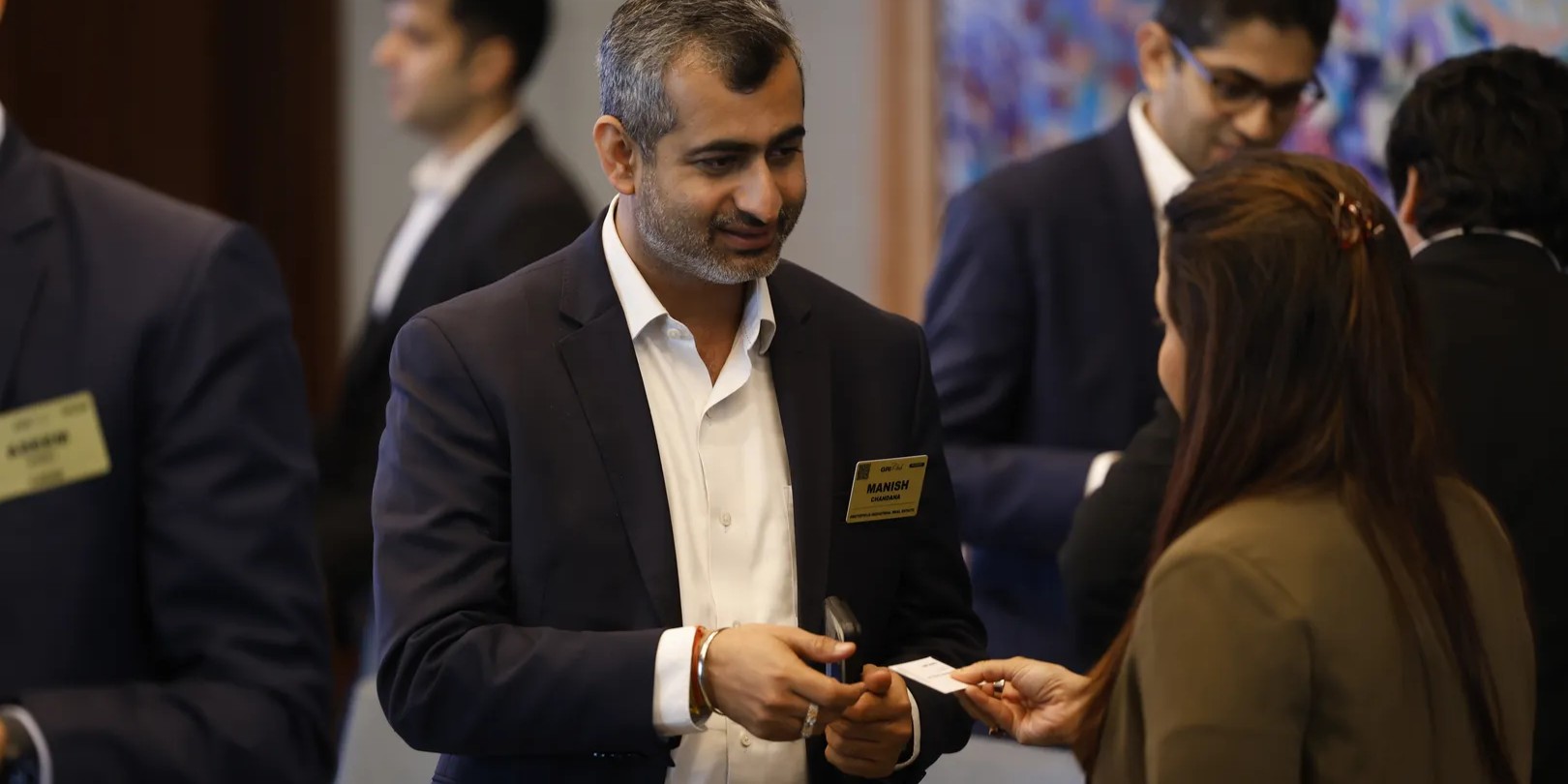
(GRI Institute)
Financial viability and cost-effective strategies
Developers and businesses are exploring financial models and design innovations to ensure projects remain viable, with strategies such as creative building designs, efficient land use, and smaller, more agile warehouses gaining momentum.Stakeholders face a key choice between CapEx-heavy models, involving significant upfront investments in land and construction, and approaches focused on operational expenditure (OpEx), which prioritise flexibility through leasing and operational expenses.
CapEx largely suits large firms with stable demand, while OpEx models are more likely to appeal to businesses needing scalability amid market uncertainty.
Innovative solutions include repurposing underutilised urban spaces, such as malls and industrial sheds, into cost-effective warehouses. Partnerships between developers and tenants also help share resources and reduce costs.
These initiatives are crucial for balancing the need for additional warehousing space with the rising costs of land and infrastructure. However, the long-term sustainability of these models remains a concern.
High operational costs in urban areas continue to make it difficult for businesses to achieve a return on investment that justifies the construction and upkeep of these facilities.
Technological advancements
Technological advancements are reshaping in-city warehousing, helping businesses keep pace with the growing demands of e-commerce, quick-commerce, and omnichannel retail while driving operational efficiency.Advanced data analytics and artificial intelligence are playing a vital role in optimising route planning, forecasting demand, and improving supply chain management, while smart inventory systems provide real-time stock updates, allowing companies to better manage inventory and reduce the risks of stockouts and overstocking.
Automation technologies, such as robotic picking, sorting, and packing, further streamline operations by reducing labour costs and increasing throughput. This automation speeds up fulfilment processes and minimises human error, leading to more accurate and reliable deliveries.
Alongside operational gains, many companies are incorporating green technologies like solar-powered warehouses and energy-efficient systems. These sustainable innovations not only boost efficiency but also contribute to reducing the environmental impact of urban logistics.